来源: 高科技与产业化
“在2021年召开的两院院士大会上,***总**提出了七个需要当下中国科学界解决的科技问题,冲锋在前的便是石油天然气。在当下,石油天然气作为国家急迫需要和长远需求,亟需科研工作者进一步科研攻关。”
周守为
近日,在青岛召开的2021世界海洋科技大会上,中国工程院院士、中国海洋学会副理事长、油气藏地质及开发工程国家重点实验室主任周守为就“深海一号”能源站作报告。他指出,“深海一号”的研究是要对标解决国家难题,尽最大可能向国家输送工业粮食——石油和天然气。
革新海洋石油工业,迈向超水深时代
“深海一号”能源站尺寸巨大,总重量超过5万吨,最大投影面积相当于两个标准足球场大小。总高度达120米,相当于40层楼高,最大排水量达11万吨,相当于3艘中型航母。其船体工程焊缝总长度高达60万米,可以环绕北京六环3圈;使用电缆长度超800公里,可以环绕海南岛一周。该项目在建造阶段已经实现3项世界级创新,运用13项国内首创技术,攻克十几项行业难题,是中国海洋工程建造领域的集大成之作。
周守为介绍:“这个钢铁巨人远不止大。它按照30年不回坞检修的高质量设计标准建造,设计疲劳寿命150年,可抵御百年一遇的超强台风。”而且在建造过程中采取无死角安全网格化
管理,取得1700万工时无事故的骄人成绩;实现高精度合龙,累计公差仅40毫米,在同类工程中世界罕见。
这一可载入史册的“钢铁巨人”在青岛建造场地日益成型之时,另一场创历史的海底施工正在南海上演——海油人进入最深的海,铺最深的管,在海底**最深的桩……其中,海管铺设首次迈进1542米水深,并创造了单日3.42公里铺设效率新纪录,仅用5天就完成了7套深水海管终端结构安装作业。
周守为介绍道,“深海一号”位于我国海南岛东南面以北150公里的东南陵水海域,水深可达1500米,其气田资源量、地质储量均超过1000亿立方米。如果一个普通三口之家一个月消耗天然气25~30方,每年消耗天然气约300~360方,那么“深海一号”大气田探明的储量换算下来可以供100万户居民使用300年左右。若气田依托海上天然气管网大动脉,每年为粤港澳等地供应30亿方天然气,便可满足大湾区约1/4民生用气需求。
“深海一号”大气田于2014年被勘探发现,并于2021年6月25日正式投产,最大水深超过1500米,最大井深达4000米以上。气田由东区和西区两部分组成,共部署11口开发井。是我国迄今为止自主发现的水深最深、勘探开发难度最大的海上超深水气田。“深海一号”的修建竣工也证明了中国海洋石油工业从此迈入超水深时代。
业内人士认为,国际上一般将水深超过300米海域的油气资源定义为深水油气,1500米水深以上称为超深水。深水是全球油气资源重要的接替区,全球超过70%的油气资源蕴藏在海洋之中,其中40%均来自深水。
为确保“深海一号”大气田顺利开发,中国海油采取了“半潜式生产平台+ 水下生产系统+海底管道”的全海式开发模式,并设计制造了全球首座10万吨级深水半潜式生产储油平台——“深海一号”能源站。
“深海一号”的背后,彰显着无数的中国智慧。“自立自强设计运作,开创了三项世界级创新。这三项创新,是高水平科技自立自强的典范。”周守为说。
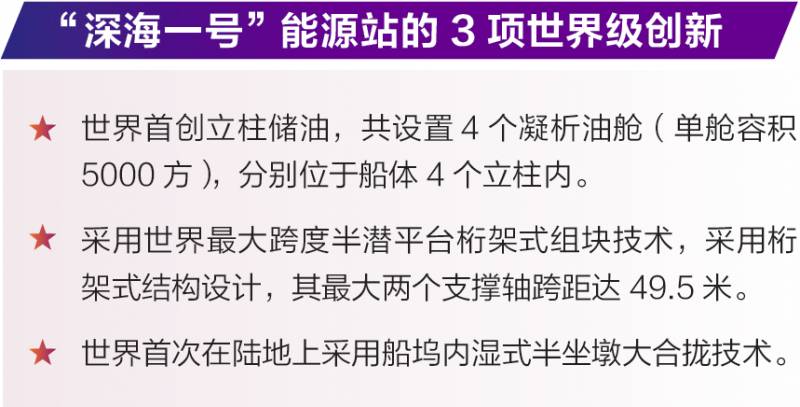
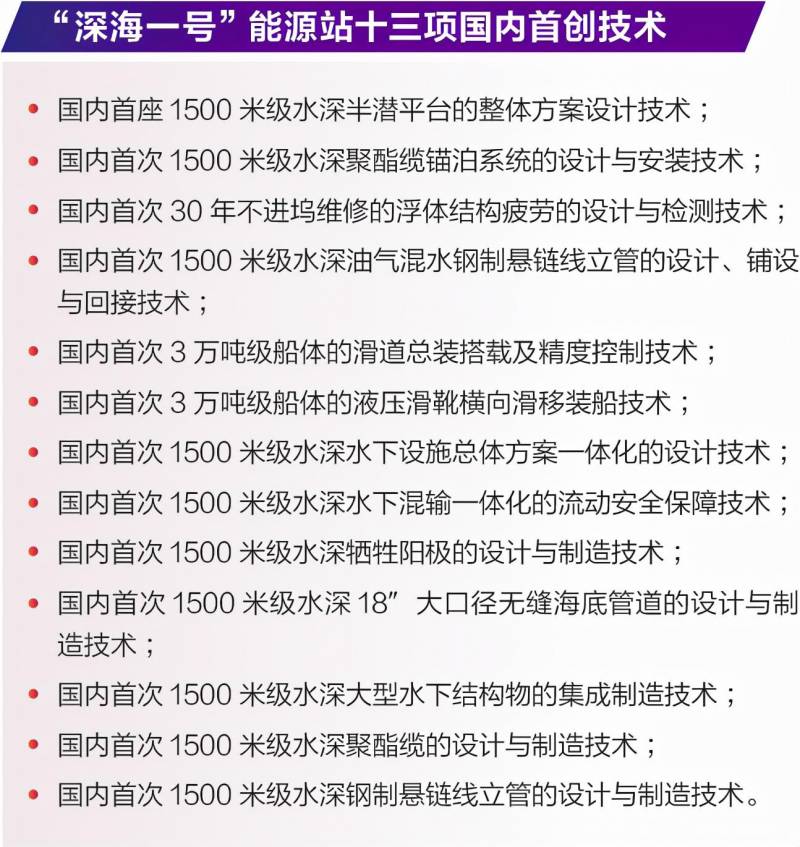
创新一:
开发多功能立柱,实现生产储油二合一
长期以来,全世界进行深海油气田开发的经典模式多为“生产平台+ 储油生产系统+ 穿梭油轮”三部分组成,该模式将生产、储存分开,将生产出的油气储存在船上,天然气运至岸上,而原油则通过穿梭油轮实现输送。
“深海一号”在世界范围内首创将深海油气田的生产、储存合二为一。不仅在投资费用上直接节省出了10~15亿元的工程投资费用,也更方便统一的生产管理。
创新背后,凝聚着深刻的科学内涵。要实现这样的合二为一,靠的是“10万吨级的半潜式深水储卸油生产平台”。周守为介绍道:“我们知道船浮在海面是因为有压载系统,当需要船上升时,就将水的压载减少,反之则增加。这一操作同样被运用在以往的深海石油气生产模式中”,过去压载水储存在四个大立柱中,而这次重大的创新便是让立柱既可以进行压载水,同时还能进行储油生产,甚至承担了部分油气处理的工作。
一个立柱高60多米,横截面逾400m2,在储油的功能之上进一步增加了油气生产的装置,一个柱子含72个舱室,设计的复杂程度可想而知。
他指出,不只是设计上的复杂,在组装上团队也曾面临不小的难题。立柱的浮体由82个分段组成,其中62个分段在海洋建造,单是每个浮体就已经十分庞大。一个分段的横截面面积是400多m2,高度为10~20米。团队需要将62个浮体分段,分船七次运输,才终于把它运到了青岛海洋工程产地进行组装,并最终在烟台完成组装。
创新二:
利用动态定位技术,实现半漂浮精准合拢
立柱组装完成后,下一步面临的挑战便是将接近2万吨的结构物放到60多米高的大型浮体上。这一庞大的结构物比足球场还大,并且四个立柱在水中处于大变形状态,相当于四条腿都已张开,而最终的组装精度不可超过13毫米。这该如何实现?
“深海一号”能源站对涂装质量和精度控制有着非常严格的要求,组块和船体连接点间距不得超过6毫米。通过成功实施合龙工程,我国半潜平台船体总装快速搭载和精度控制技术已达到世界先进水平,多项深水施工技术突破1500米难关,全面掌握了中心管汇等10余种水下关键装备的自主制造技术,超大型深水装备工程总包能力显着提升。同时,该项目还引进了人员定位系统,无死角开展安全网格化管理,克服受限空间作业多、交叉作业多等难题,取得了1700万工时无事故的骄人成绩。
除此之外,为把这个比足球场还大的结构组织吊起来,团队采用了分组排式的吊点技术。24个吊点和48根钢缆共同配合,实现了这一世界首创的半浮漂精准合拢实践。
创新三:
开创预回正横向转移技术,让让浮体“安全着陆”船体
“解决了组装的各个难题,还有一个装配上船的困难摆在面前。”周守为介绍道,“浮体共有三万多吨,如何实现运行上船?”
在世界范围内,一般采用的都是船尾上船的方式,但由于“深海一号”的组件实在过于庞大,足有3万多吨,如果全部压在船尾,就将造成船的结构问题。于是便采用了横向装船,依靠滑轨的作用,给船铺上钢轨,再通过液压将其运到大船上,等浮体上来以后,再慢慢让位置趋于平衡,这个过程开创了结构的预回正横向转移技术。
从“深海一号”研发设计到投入使用的过程中,共创造出三项世界首创和十三项国内首次,但在周守为看来:“不管实现了多少个首次或创新,任何工程创新都必须以安全设计安全作业为基础”。在组件合拢后,需要将“深海一号”从烟台运送到陵水气田,整个路程将近1609海里,最终这个庞然大物提前三天被运送到中国南海的目的地。
周守为总结道:“海上没有路,但是海上又到处都是路,而且没有一条重复的路,我们有信心有决心走出一条符合中国特色的海洋强国之路。”这条路,是加快进军深海步伐,不断实现油气增产的路;是突破“卡脖子”技术、绿色能源转型的路;更是革新石油海洋工业、海洋工程的路。
知领,中国工程院中国工程科技知识中心官方订阅号。关注科技动态,普及科技知识,弘扬院士精神,传播科学思想。